在制造业的智能化浪潮中,数控技术正成为推动精密加工与高效生产的关键引擎。本文将从核心技术、应用场景及未来趋势等多维度展开解析,为从业者提供兼具深度与实用性的参考。
一、数控技术的核心组成:从概念到模块
1. 数控技术的定义与发展
数控技术(Numerical Control)是一种通过数字化指令控制机械运动的技术,融合了机械制造、计算机科学、传感检测等多领域技术。自20世纪50年代诞生以来,其发展经历了从简单指令控制到智能化集成的跨越。例如,德国西门子与日本FANUC的数控系统已成为全球工业标准,而我国通过引进与自主研发,逐步在高端市场取得突破(如沈阳机床的i5智能系统)。
2. 数控机床的四大核心模块
数控系统(CNC系统):相当于机床的“大脑”,负责解析程序并协调各部件。其核心功能包括指令处理、运动控制和实时反馈,典型代表如FANUC的CNC装置。
伺服系统:由伺服电机、驱动器和编码器组成,将数字指令转化为精准的机械运动。例如,高脉冲频率(可达500K以上)的伺服系统能够实现微米级加工精度。
机床本体:包括床身、导轨、主轴等结构件,其刚性与稳定性直接影响加工质量。德国机床以高强度铸铁床身和精密导轨著称,而国产机床在轻量化设计上逐步追赶。
测量与反馈系统:通过光栅尺、编码器等传感器实时监测位置与速度,形成闭环控制以修正误差。例如,海德汉的高精度光栅尺被广泛应用于航空航天领域。
二、数控技术的应用价值:效率与精度的双重突破
1. 高精度加工场景
数控机床可通过多轴联动(如五轴加工)实现复杂曲面加工,误差可控制在0.001mm以内。典型案例包括航空航天发动机叶片、医疗器械植入物等。
2. 生产效率提升
自动化换刀与多工序集成:加工中心通过刀库系统实现多工具自动切换,减少人工干预。例如,某汽车零部件生产线采用数控机床后,效率提升300%。
柔性生产适应性:通过修改程序即可切换加工对象,适用于小批量定制化生产,如模具制造与3C电子产品加工。
3. 节能与成本优化
数控机床通过智能调速、负载检测等功能降低能耗。例如,某企业引入数控系统后,综合能耗下降15%,刀具寿命延长20%。
三、未来趋势:智能化与开放化
1. 工业4.0与智能化升级
数字孪生与预测性维护:通过物联网传感器采集数据,构建设备虚拟模型以预测故障。例如,某企业利用机器学习分析主轴振动数据,减少停机时间30%。
AI驱动的工艺优化:智能算法可自动生成加工路径并调整参数。如某开源项目(如STM32F407 GRBL)支持六轴协同控制,兼容AI优化模块。
2. 开放式数控系统生态
开源平台的应用:基于LinuxCNC、GRBL等开源框架,中小型企业可低成本实现定制化开发。例如,某雕刻机厂商通过修改GRBL源码,将成本降低40%。
云数控与边缘计算:通过云端协同实现远程监控与程序分发,结合边缘计算降低延迟。例如,某工厂通过云平台管理全球50台设备,故障响应速度提升60%。
四、实用建议:企业如何高效落地数控技术
1. 技术选型策略
匹配需求选择系统:中小批量生产可选FANUC或华中数控的中端系统;精密加工则需西门子Sinumerik等高精度方案。
重视核心部件兼容性:确保伺服电机、导轨等与数控系统匹配,避免性能瓶颈。例如,日系伺服电机更适合高速场景,而欧系产品长于重载。
2. 优化生产流程
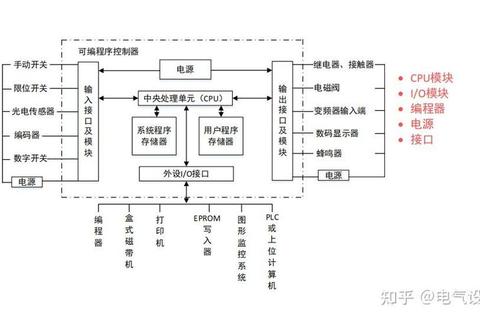
编程标准化:采用模块化G代码设计,减少重复劳动。例如,使用宏程序实现常见工艺(如倒角、螺纹)的快速调用。
数据驱动的维护:建立设备运行数据库,通过OEE(设备综合效率)指标分析瓶颈环节。
3. 人才培养与协作
跨领域技能培训:操作人员需兼具机械加工与基础编程知识。建议与职业院校合作开展“数控+IT”双技能课程。
产学研合作:联合高校研发定制化数控模块,例如某企业与高校合作开发五轴联动算法,加工效率提升25%。
数控技术正从单一设备控制向全产业链智能化演进。企业需紧跟技术趋势,结合自身需求优化设备与流程,方能在制造业转型升级中占据先机。通过核心技术的深度理解与策略性应用,数字化控制与机床自动化将成为推动“中国智造”的核心动力。
相关文章:
文章已关闭评论!